Forward:Making sure your slippers are consistently made with good quality is important. You want to have a good brand reputation, make your customers happy, and build a long-term relationship with your customers. To do that, you need to know how manufacturers make sure the slippers they make for you are made well so you can buy with confidence.
1. Establishing Clear Quality Standards
- Define Specifications:You start with the specifications for your slipper. You need to tell the manufacturer what materials you want them to use (fabric, foam, rubber soles, etc.), what sizes you want, how much they should weigh, what the stitching pattern should look like, and what colors they should be. Those are your specifications. That’s your definition of quality. That’s what
keeps you from getting a bunch of slippers that look different from one batch to the next.
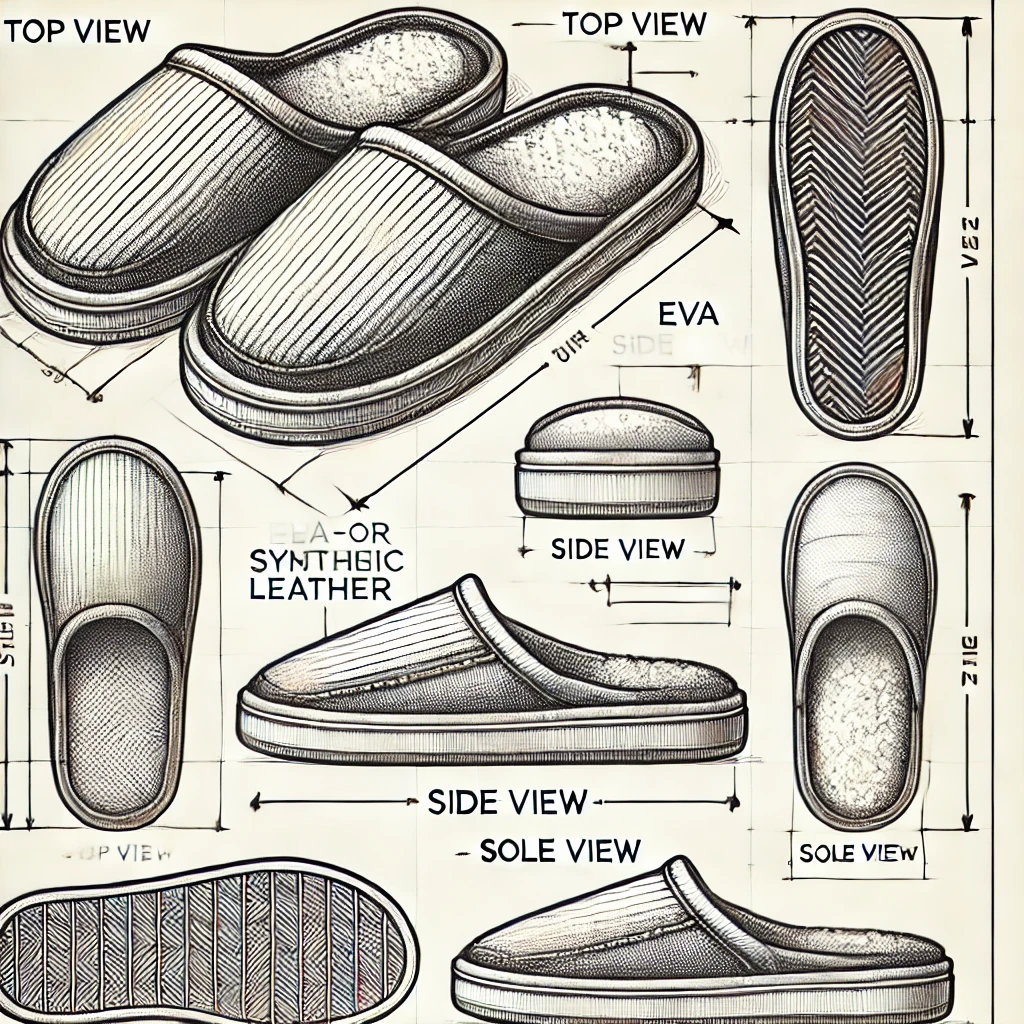
- Quality Control Checklist: Next, you create a quality control checklist. You create a list based on
your specifications of what the inspectors are supposed to look for at each stage of production, from selecting the raw materials to the final packaging.
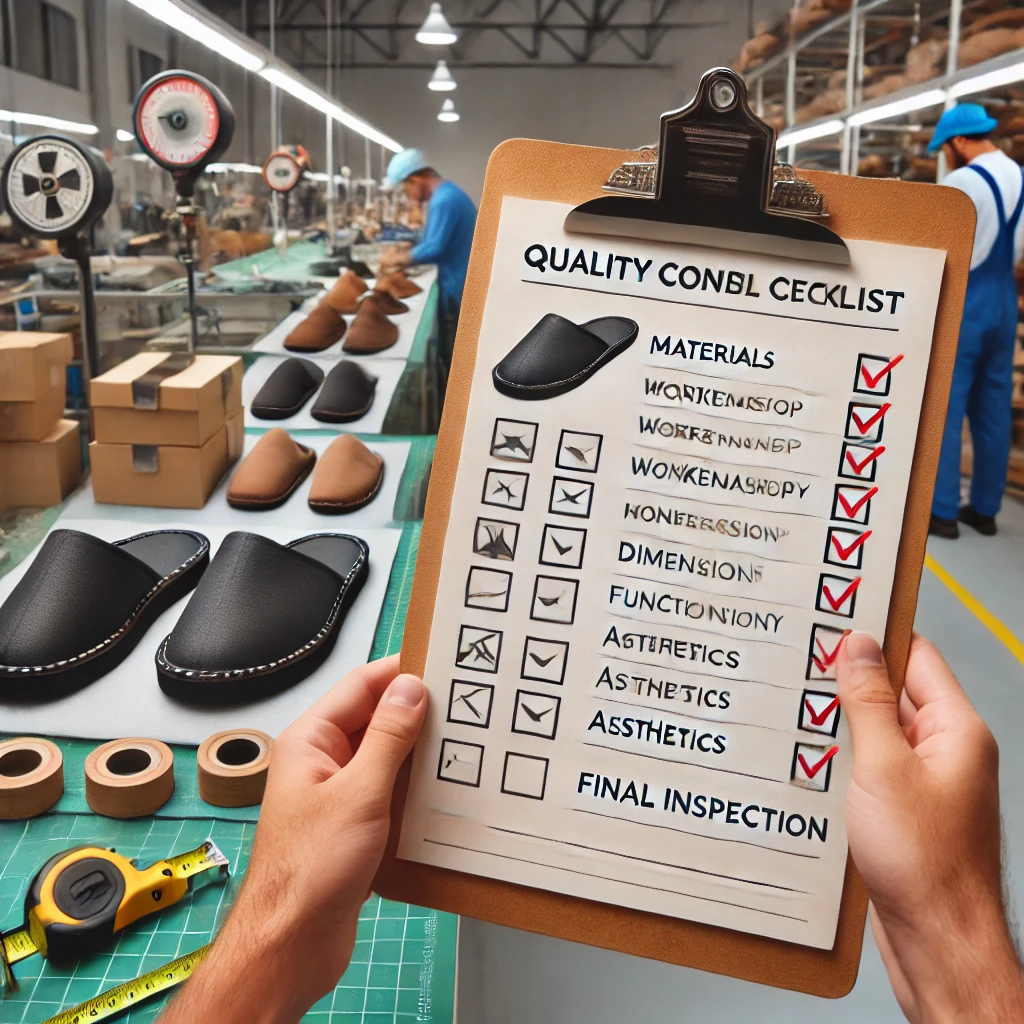
- Set Tolerance Levels: Some minor variations in product dimensions or weight might be acceptable, but these need to be clearly defined. For example, a size 9 slipper might have a +/- 0.5 cm tolerance in length.
2. Supplier and Material Control
- Sourcing from Trusted Suppliers: Quality starts with your raw materials. You want to use suppliers who have a track record of providing good quality. For example, the foam you use for your slipper soles should come from a reputable source that has good quality foam. The fabric you use for the uppers should come from a reliable source that has high-quality fabric.
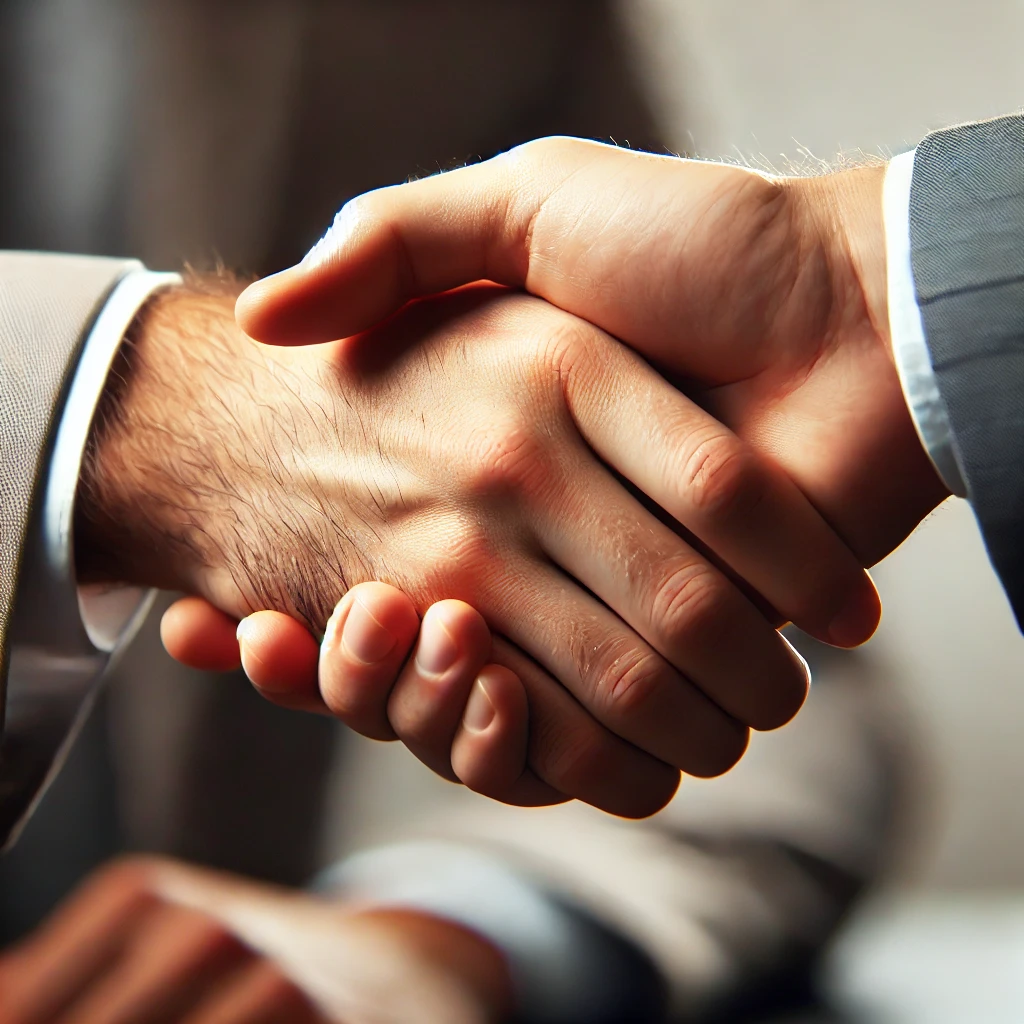
- Supplier Audits: Regular audits of material suppliers ensure they maintain high-quality production standards. This could include checking their manufacturing processes, their own quality control measures, and their adherence to any regulatory standards (e.g., environmental, labor practices).
- Material Testing: Slippers are made from a variety of materials, including rubber, fabric, foam, and synthetic fibers. All of these materials need to be tested for durability, elasticity, comfort, and safety. For example, you might test for toxic substances in the dyes or adhesives to make sure they comply with safety regulations in the countries where you sell your slippers.
3. Production Process Control
- Standardized Manufacturing Processes: Manufacturers must implement standardized procedures at every stage of the production process. From cutting fabric to assembling the soles, each task should be done following precise guidelines to ensure consistency.
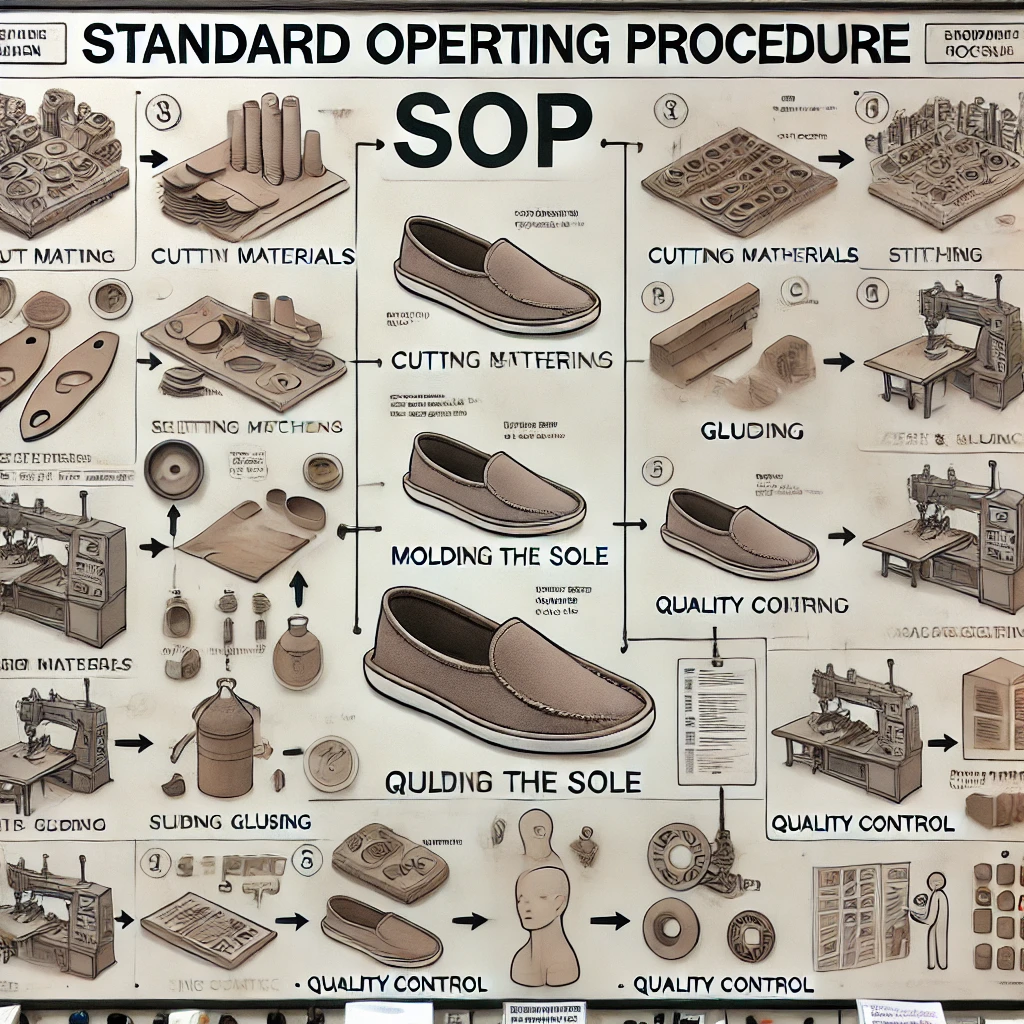
- Invest in Automation: Where possible, you want to use automation to increase precision and
reduce human error. For example, you might use an automated cutting machine to cut pieces of fabric or foam to make sure they’re all the same size. That’s hard to do by hand.
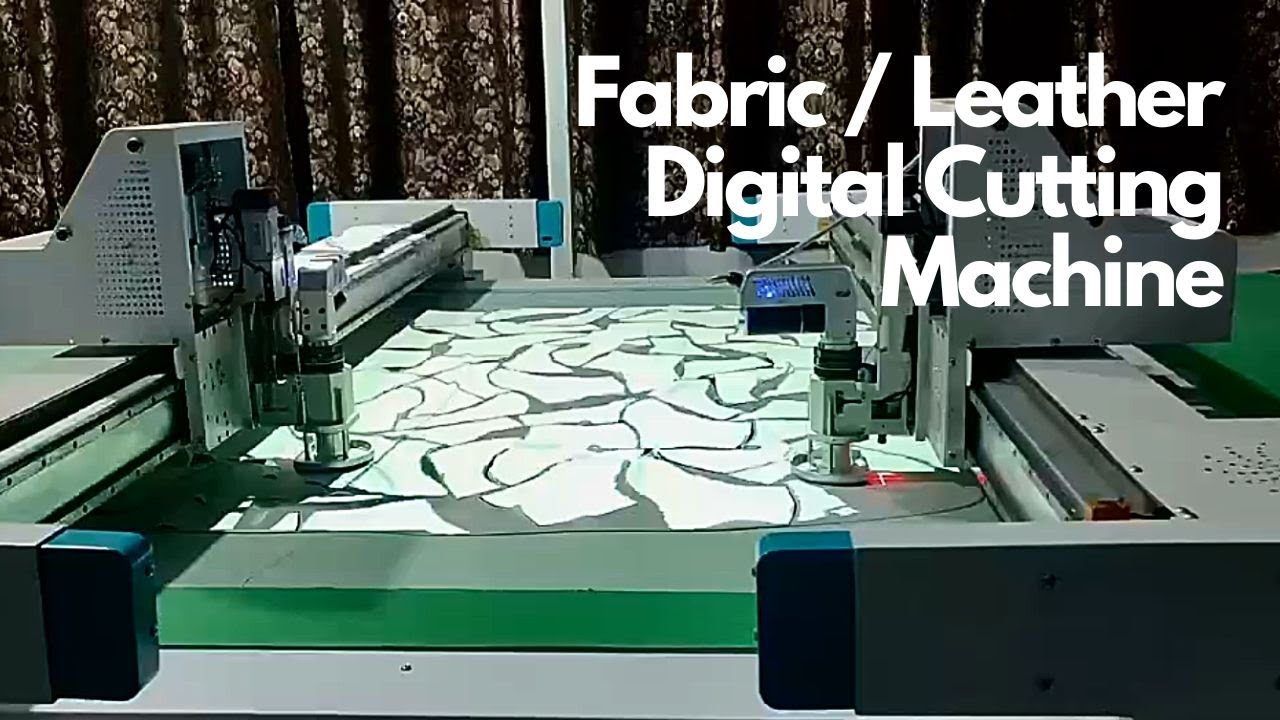
- Worker Training: Even in partially automated processes, workers play a critical role in maintaining quality. Regular training ensures that workers understand the importance of following procedures precisely. Well-trained workers are also more likely to identify defects and address issues on the production line.
4. In-Line and Final Quality Inspections
- In-Line Inspections: Quality control should not wait until the final product is ready. In-line inspections at key stages of production help identify issues early. For example, checking the uniformity of materials after cutting or inspecting stitching quality before the soles are attached can prevent defects from advancing further down the production line.
- Final Quality Inspections: Once the slippers are fully assembled, final inspections are necessary before they are packaged and shipped. These inspections should focus on overall appearance, correct sizing, weight distribution, stitching quality, sole attachment, and other customer-facing features.
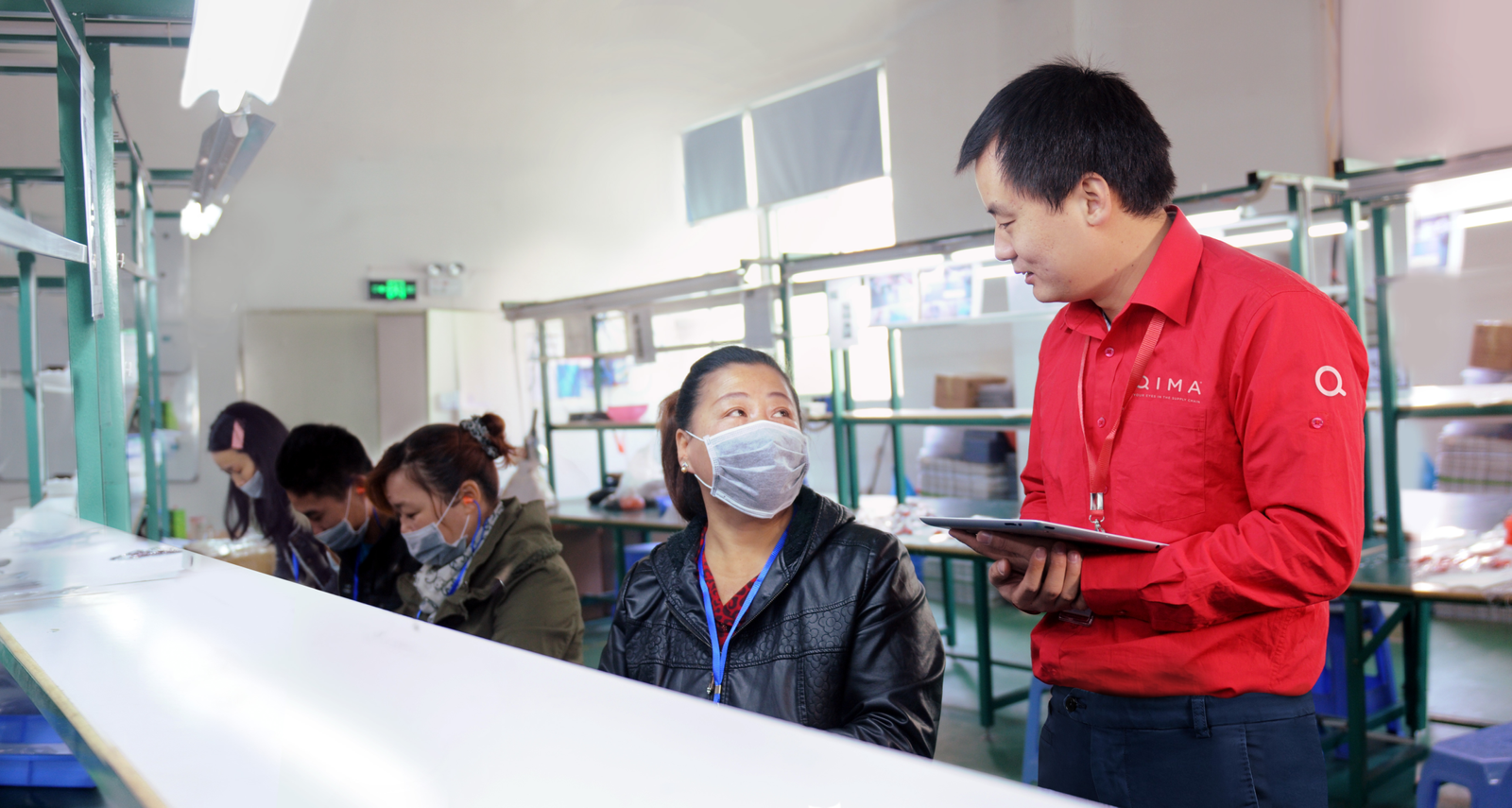
5. Quality Assurance Systems
- Implement ISO or Other Relevant Standards: Adopting international quality standards, such as ISO 9001, can help structure a manufacturer’s quality management system. These standards provide frameworks for maintaining and improving quality over time, covering everything from production processes to customer feedback.
- Quality Control Software: Modern manufacturers use quality control (QC) software to monitor production metrics in real time. These systems can track defects, downtime, material wastage, and process bottlenecks, providing insights into areas for improvement. For example, if you see a spike in defective soles, that might tell you that you have a problem with a machine or a supplier. It helps you get quick corrections in place.
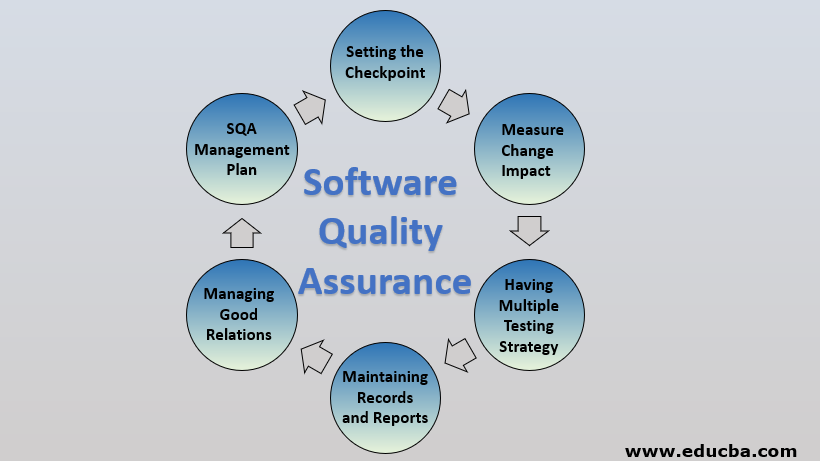
6. Product Testing
- Durability and Comfort Testing: Slippers should be tested for durability, particularly in areas like the sole and stitching, which endure the most stress. Comfort is another critical factor. Wear tests can be conducted to measure comfort levels and identify potential issues, such as materials that cause irritation or poor arch support.
- Safety Testing: Slippers should comply with all relevant safety standards, particularly if they are being sold in international markets. For example, flammability testing and checking for harmful chemicals in materials should be standard procedures, especially when the slippers are intended for children.
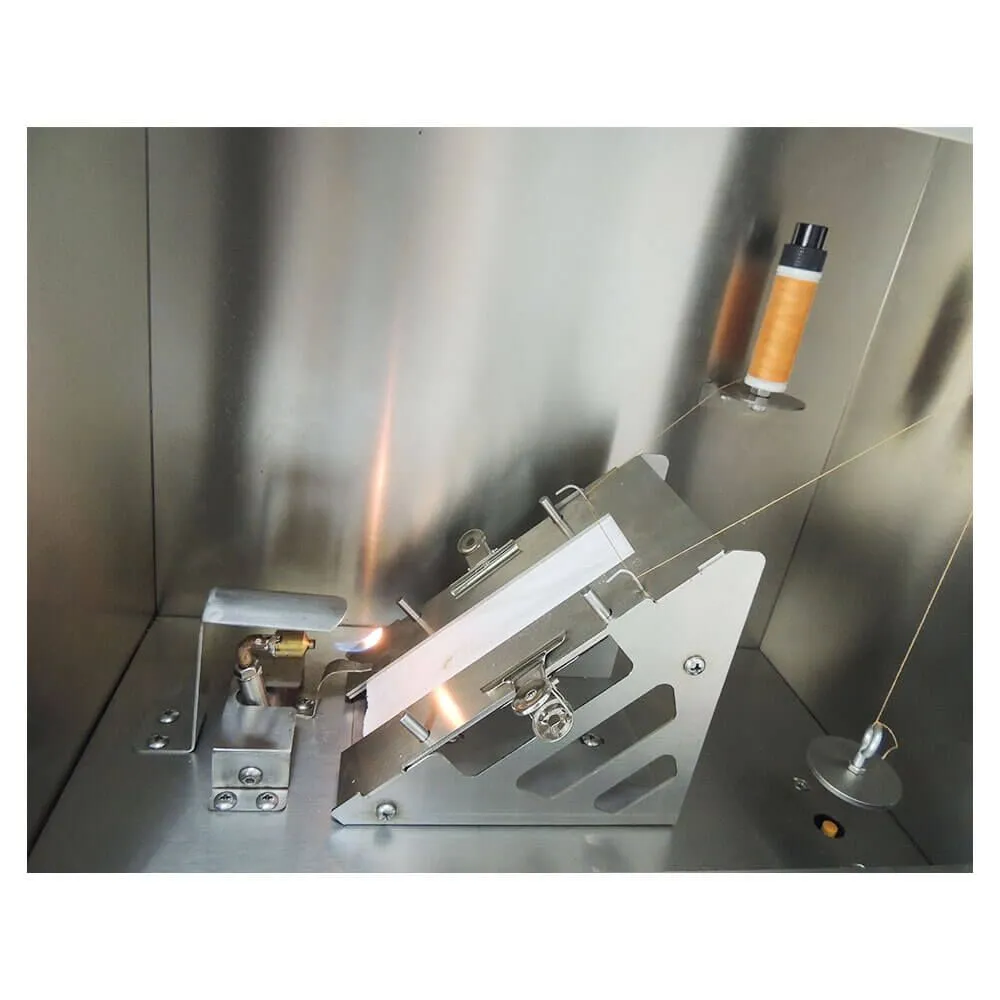
- Environmental Testing: In some cases, manufacturers may need to ensure that slippers can withstand various environmental conditions, such as heat, cold, or moisture. This is especially important for outdoor slippers or those intended for wet areas like bathrooms.
7. Continuous Improvement and Feedback Loops
- Customer Feedback: Consistent quality doesn’t stop at the factory floor. Retailer and customer feedback is vital for long-term improvement. Customer reviews, return data, and direct feedback should be collected and analyzed to identify common issues (e.g., premature wear, sizing inconsistencies).
- Supplier Feedback: You need to have good communication with your suppliers. If you have consistent defects in your slippers, and you trace that back to a specific material, you need to tell your supplier. They need to take corrective action. It might involve changing how they make the material or finding a different material that meets your standards.
- Internal Reviews and Audits: Manufacturers should regularly review their own processes and quality control systems to identify areas for improvement. Audits can help pinpoint inefficiencies or weaknesses in the current production process that may lead to quality variations.
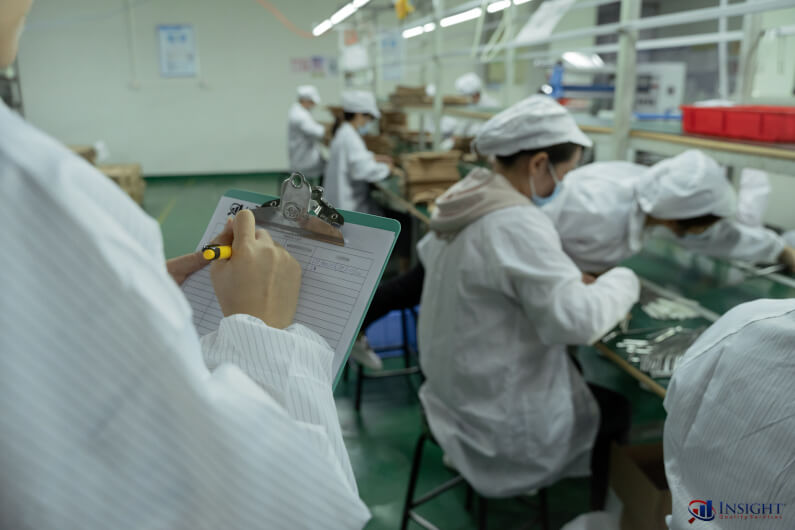
8. Packaging and Shipping Standards
- Protective Packaging: Slippers must be packaged carefully to prevent damage during transport. Poor packaging can result in bent soles, crushed uppers, or other defects. Packaging should also protect against environmental factors such as moisture.
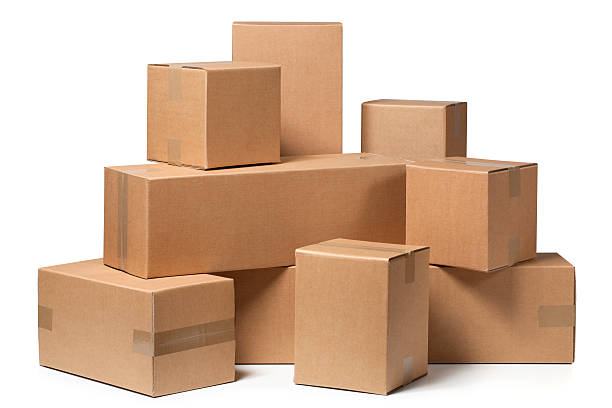
- Consistency in Branding and Labels: Packaging should include all necessary labels, barcodes, and branding elements consistently. Inconsistent labels or missing information can affect the brand’s image and lead to delays at the retailer level due to scanning issues or incorrect inventory tracking.
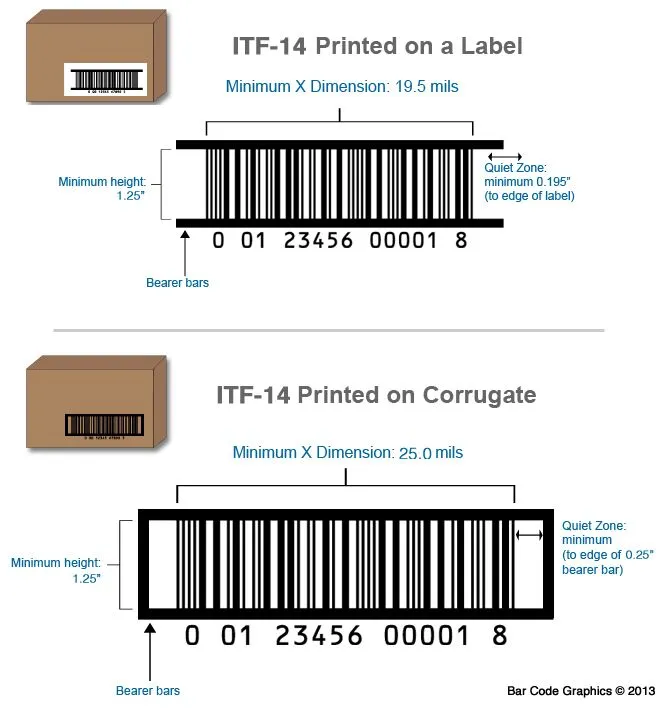
- Shipping Conditions: Slippers are generally light and they’re not going to break, but they can
still have issues when they’re being shipped. You need to make sure your shipping partners understand the requirements for temperature control, handling, and storage. This is especially important when you’re shipping your slippers internationally.
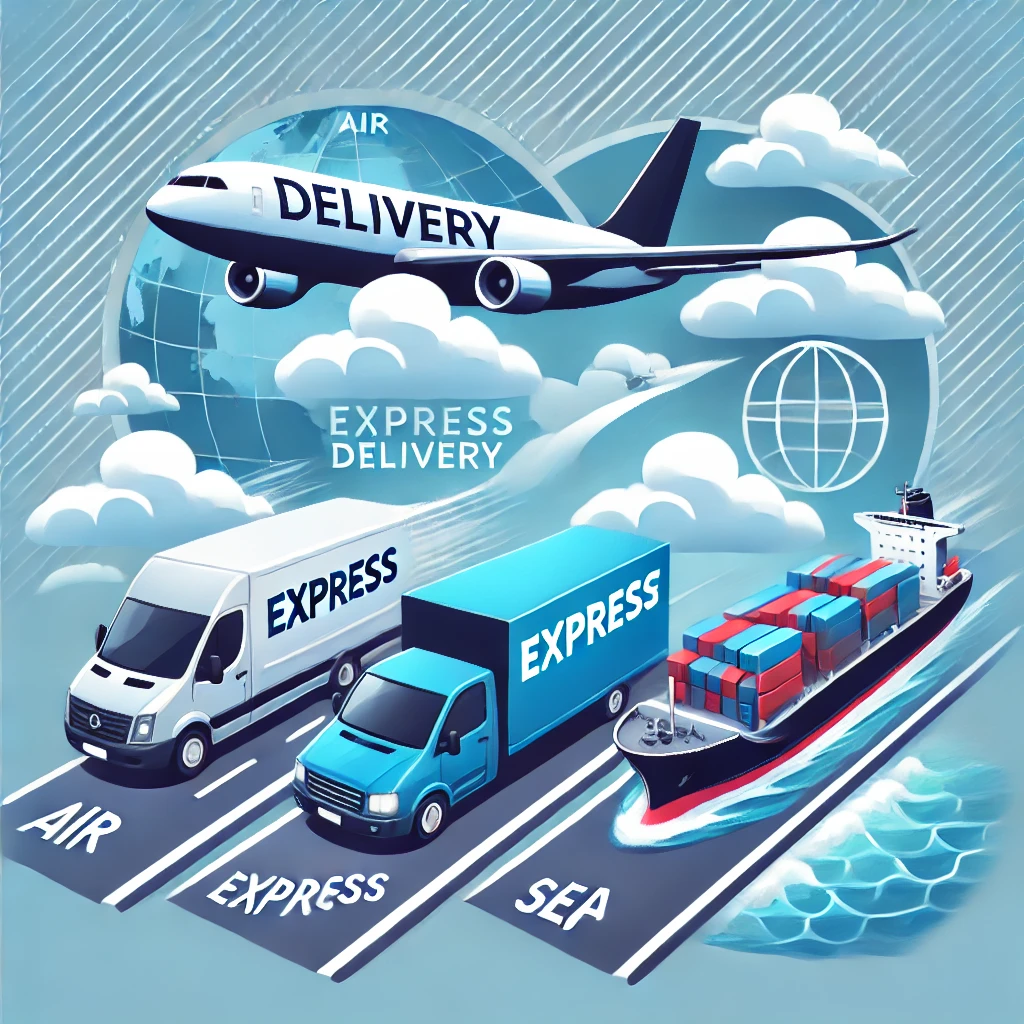
9. Compliance with Regulatory Standards
- Environmental Regulations: Manufacturers need to comply with environmental regulations, such as the use of non-toxic materials and eco-friendly production methods. This is particularly important for customers and markets that prioritize sustainability.
- Labor and Safety Standards: Compliance with labor laws, including fair wages and safe working conditions, is crucial. Ethical production not only enhances the brand’s reputation but also helps avoid disruptions in production due to legal issues.
- Import/Export Regulations: For international shipping, ensure compliance with the regulations of the destination country. This includes safety standards, labeling requirements, and import tariffs, which can vary significantly by region.
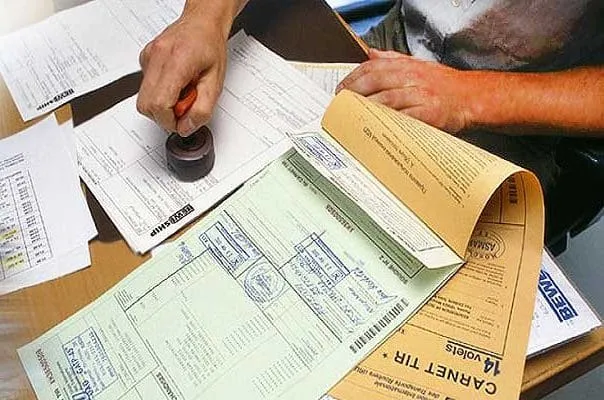
10. Cost Control Without Compromising Quality
- Optimize Material Usage: You can use software and modern machinery to help you cut and use
your materials more efficiently. For example, an automated cutting machine can reduce fabric waste by as much as 30%. That’s a way you can save money without sacrificing quality
- Lean Manufacturing Techniques: Applying lean manufacturing techniques helps reduce waste and inefficiencies in production. By streamlining processes, manufacturers can maintain high quality while keeping costs low.
- Strategic Supplier Relationships: Building strong, long-term relationships with suppliers can result in better prices for high-quality materials. Bulk purchasing or long-term contracts can reduce material costs without compromising on quality.
Conclusion
Consistent quality in slipper manufacturing is achieved by having good specifications, controlling your materials, having good processes, and doing a good job with quality control. As a buyer, you need to understand how each of these things works so you can evaluate your suppliers. You want to work with suppliers who are transparent, who comply with international standards, and who are always looking for ways to improve. That way, you can make sure you’re buying slippers that meet your customers’ expectations, and you can build a long-term relationship based on trust and reliability in your supply chain.