Foreward: as a buyer for a large-scale retailer or supermarket chain, ensuring the quality, compliance, and reliability of your slipper suppliers is essential. Conducting supplier audits for slipper manufacturing plants is a critical step in ensuring that your business partners adhere to industry standards, regulatory requirements, and ethical business practices. This guide will provide a simple and structured overview of what supplier audits entail, why they are essential for slipper manufacturing plants, and how you can execute them effectively.
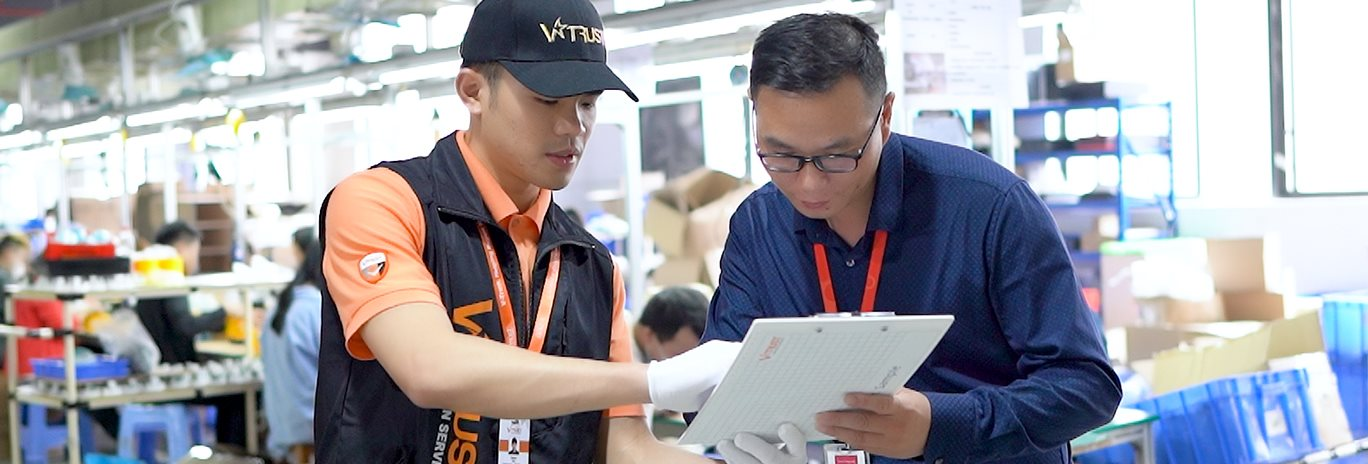
1. Why Supplier Audits Are Essential
1.1 Ensuring Product Quality
One of the reasons you might audit a slipper supplier is to check out the quality of the slippers they make. Slippers are a commodity, but just like any other consumer product, you want to make sure they don’t have issues like inconsistent sizing, poor durability, or defective materials that cause them to have high return rates and customers to be unhappy. You are going to check out the quality management systems (QMS) they have in place at the plant where they make the slippers.

1.2 Compliance with Regulatory Standards
Different countries have different rules around product safety, what materials you can use, and what you need to put on the label. For example, the European Union (EU) has regulations about what chemicals can’t be in footwear, such as phthalates or heavy metals. You are going to audit the supplier to make sure they meet these regulations so you don’t get fined, have to do a recall, or damage your brand reputation.
1.3 Ethical Practices and Sustainability
In today’s market, ethical sourcing and sustainability are becoming non-negotiable. Consumers are increasingly aware of labor practices, environmental impact, and corporate social responsibility (CSR). Auditing suppliers gives you visibility into the working conditions at manufacturing plants, their sustainability practices, and adherence to fair labor standards, which are crucial in building a responsible supply chain.
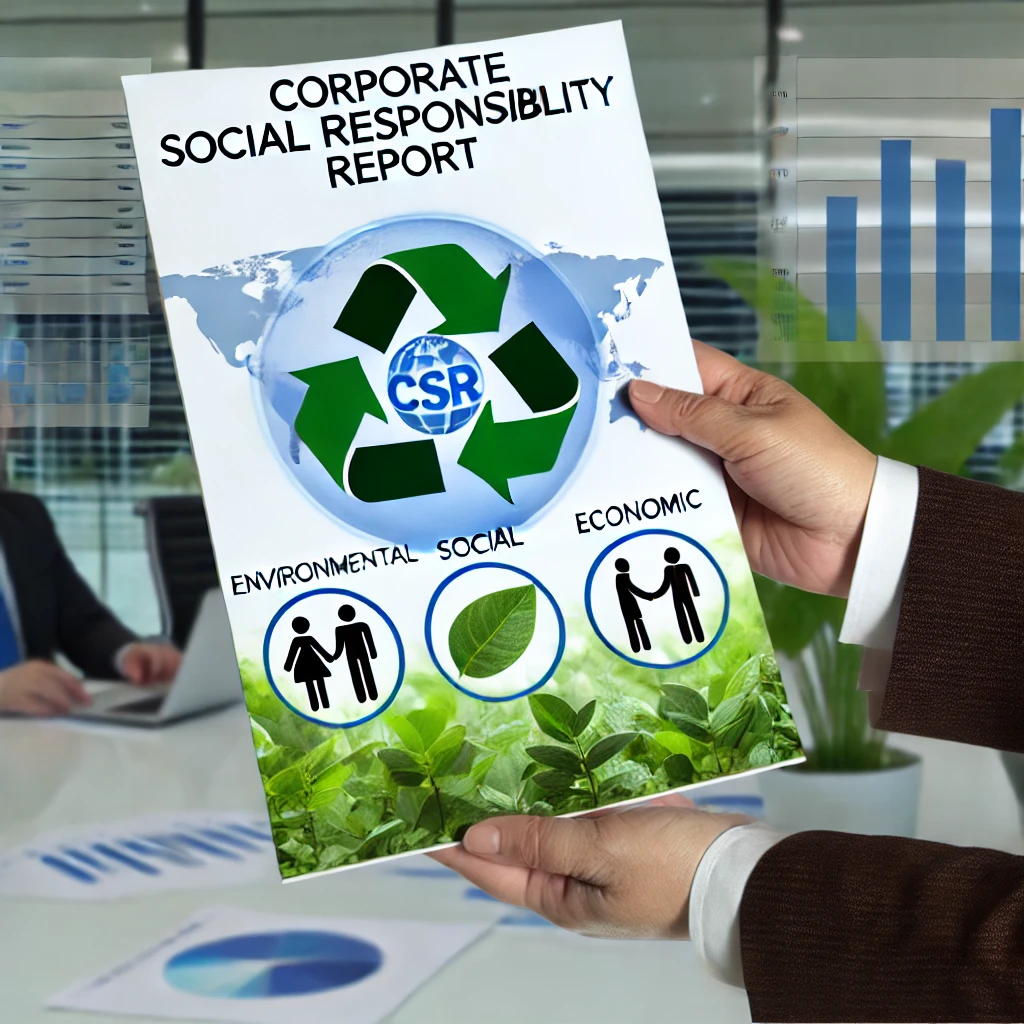
1.4 Risk Mitigation
When you audit a supplier, it’s to mitigate your risks. Risks could be things like your supply chain being disrupted. It could be the supplier you’re thinking about using is not financially healthy. It could be that they don’t have the capacity to produce what you need when you need it. Maybe they are in a country where there are risks like natural disasters or political unrest. The idea is to understand these risks so you can develop a plan to mitigate them and make a more informed decision about buying from this person.
2. Types of Supplier Audits
When auditing a slipper manufacturing plant, different types of audits can be performed based on your specific objectives. Each of these audits will target various aspects of the supplier’s operations.
2.1 Factory Audit
A factory audit focuses on evaluating the overall production capability and processes of the supplier. This includes reviewing the manufacturing processes, machinery, production capacity, and workforce expertise. For slipper manufacturing, key elements might include:
- Production line efficiency and output.
- Machinery used for cutting, stitching, and assembling slippers.
- Quality control processes during production.
- The state of maintenance and repair for production equipment.
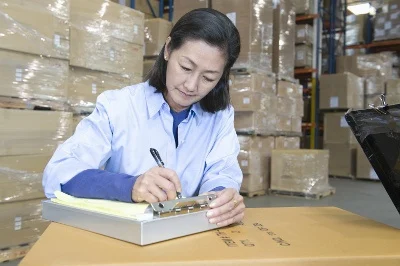
2.2 Quality Management System (QMS) Audit
A QMS audit dives deeper into the supplier’s processes for maintaining consistent product quality. This audit will assess how the supplier manages quality from raw material sourcing to final product inspection. The key focus areas here include:
- Documented procedures for quality control.
- In-process inspection points and criteria.
- Final product inspection standards (e.g., size accuracy, stitching quality, durability).
- Handling of non-conforming products and corrective actions.
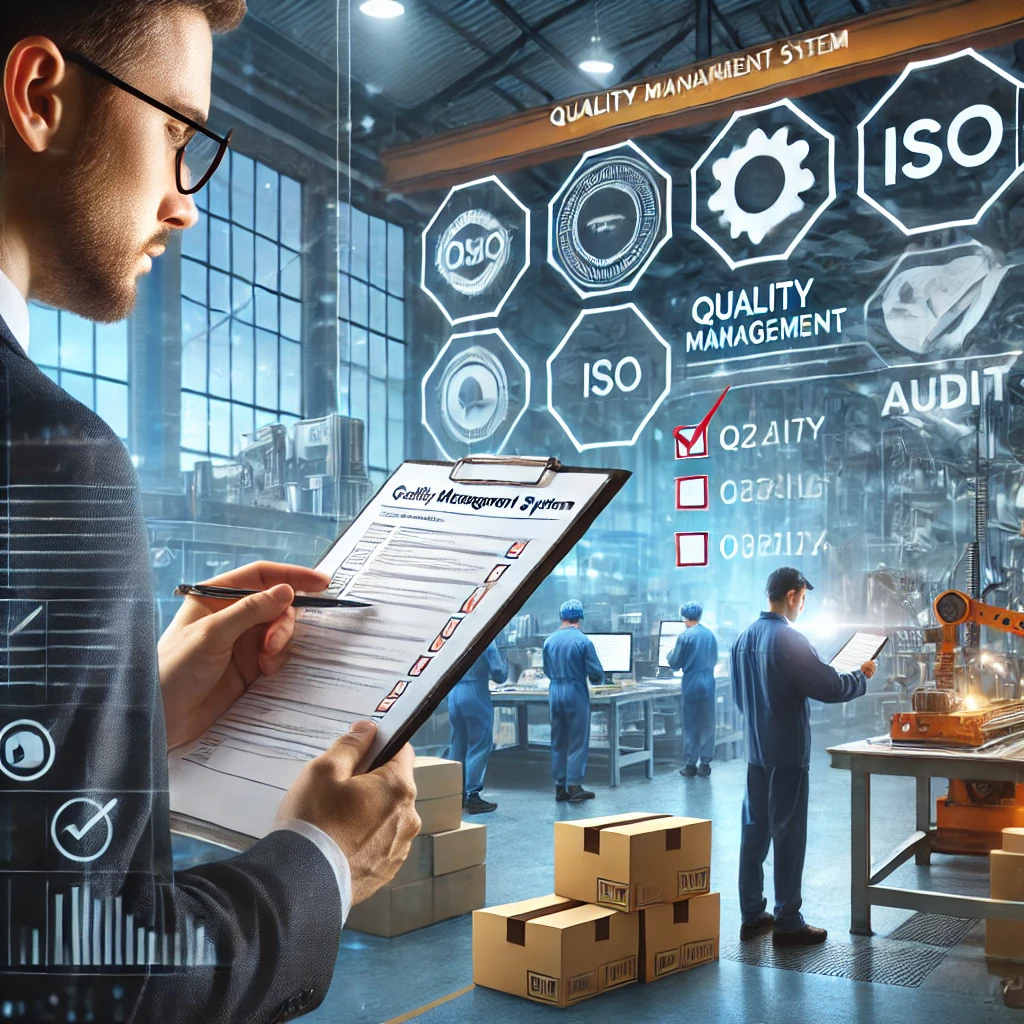
2.3 Social Compliance Audit
A social compliance audit is focused on verifying that the supplier adheres to labor laws and ethical standards. This is particularly crucial in regions where labor practices might be more loosely regulated. Elements covered in a social compliance audit for slipper manufacturing include:
- Fair wages and working hours.
- Employee health and safety measures.
- Absence of forced labor or child labor.
- Environmental responsibility, such as waste management and use of sustainable materials.
2.4 Environmental Audit
An environmental audit assesses the slipper supplier’s environmental impact, including waste management, energy consumption, and sustainability initiatives. Given the increasing demand for eco-friendly products, many retailers require suppliers to demonstrate environmentally responsible practices. Key focus areas include:
- Water usage and waste treatment systems.
- Carbon footprint and energy efficiency.
- Sustainable material sourcing (e.g., recycled rubber or organic fabrics).
- Compliance with local environmental regulations.
2.5 Financial Audit
While less common, a financial audit may be performed to assess the financial stability of your slipper supplier. If your company is entering into a long-term agreement or placing significant orders, understanding the financial health of the supplier is vital. The audit will typically review financial statements, tax filings, and any outstanding debts or obligations.
3. Key Steps in Conducting a Supplier Audit
3.1 Pre-Audit Preparation
Preparation is crucial for a successful audit. Before conducting an on-site audit, gather as much information as possible about the supplier. This can include:
- Reviewing past performance, including product quality, on-time delivery, and communication.
- Assessing previous audit reports, if available.
- Defining your specific audit objectives, whether it’s quality, social compliance, or financial health.
Make a list of the things you want to check out when you do the audit. This list should be customized to your business.
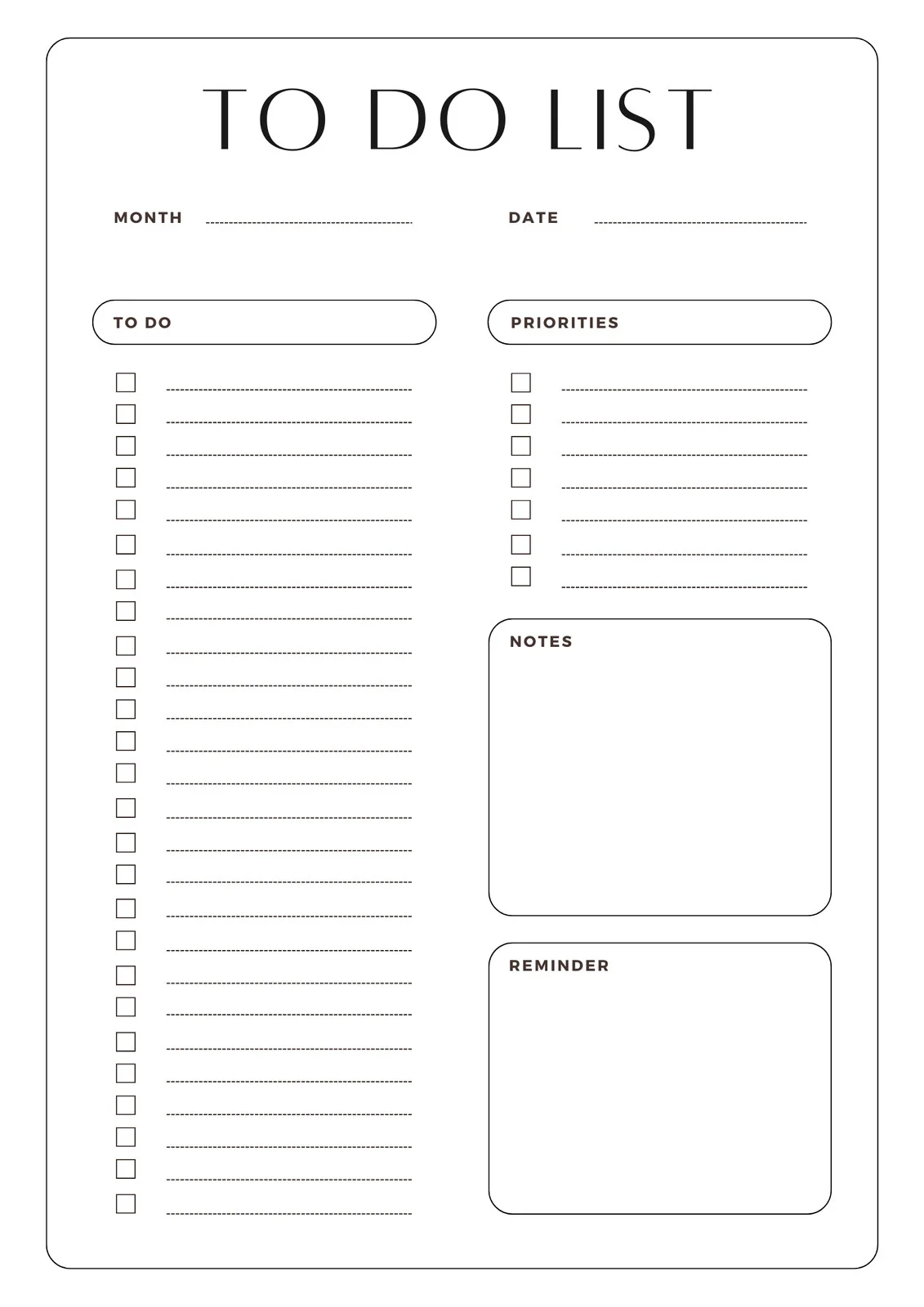
3.2 On-Site Inspection
The on-site inspection is the heart of the audit. Depending on the scope of your audit, this process can take several hours or even days. Key steps include:
- Touring the production facilities to assess machinery, workflow, and cleanliness.
- Interviewing factory staff and management to understand their processes and policies.
- Reviewing documentation such as quality control records, employee contracts, and environmental impact reports.
During the inspection, make sure to take detailed notes and photos (where permitted) to document your findings.
3.3 Assessment of Compliance
Once the on-site inspection is complete, the next step is to assess whether the supplier meets the required standards. Depending on the type of audit, this could involve:
- Comparing quality control measures to your specifications.
- Checking compliance with labor laws and ethical standards.
- Evaluating environmental responsibility.
At this stage, it’s crucial to identify any major non-conformities, areas of improvement, or risks that could affect your business relationship.
3.4 Audit Report
After you finish your assessment, put your findings into a report. This report will have the following information in it:
- Areas of compliance and non-compliance.
- Any risks or concerns identified during the audit.
- Recommendations for corrective actions or improvements.
Your report should be clear and actionable, giving the supplier the opportunity to address any issues raised.
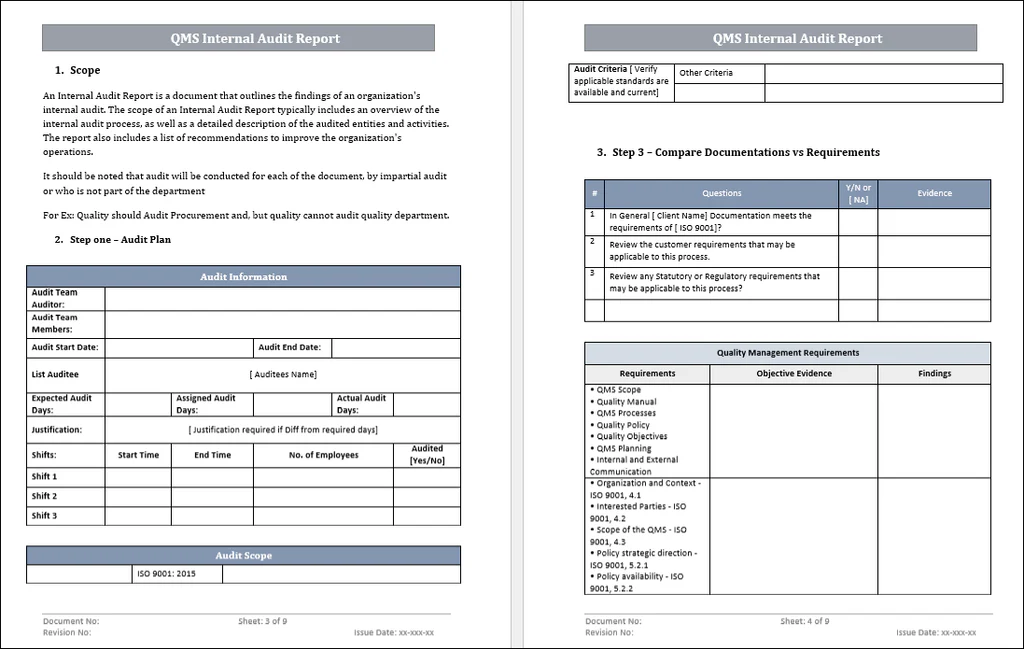
3.5 Follow-Up and Corrective Actions
If the audit identifies any significant non-compliance or risks, it’s essential to follow up with the supplier. This may involve:
- Developing a corrective action plan (CAP) with specific timelines.
- Scheduling a re-audit to verify that corrective actions have been implemented.
- Reevaluating the supplier’s performance and deciding on future collaboration.
4. Common Challenges in Supplier Audits
4.1 Language Barriers
A lot of times, your supplier is in another country. They may not speak English, so you will need an interpreter. Alternatively, you will work with an audit firm that speaks the language and is familiar with the customs in that country.

4.2 Cultural Differences
Cultural differences can also play a role in how audits are conducted. For example, there may be certain parts of the facility the supplier is hesitant to let you see. The supplier may not think issues are a big deal
that you think are a big deal. You need to have a good relationship with the supplier. You also need to be very clear about what you expect and what they should expect.
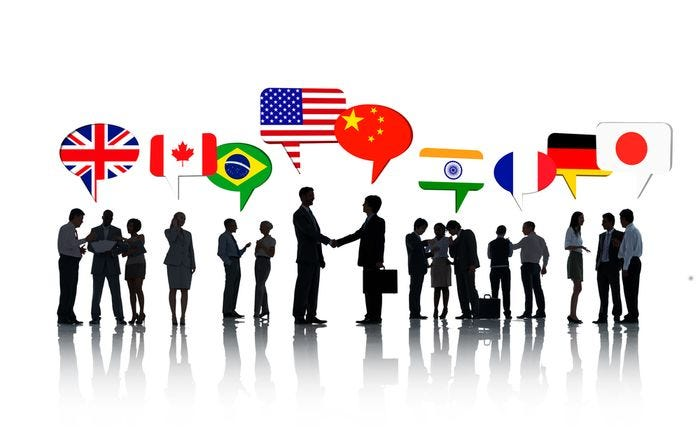
4.3 Resistance from the Supplier
Some suppliers may not want you to do an audit because they think it’s invasive or that they don’t need to be audited. You need to explain to them that you are working together to improve the quality of their product. You are looking at their quality management systems to make sure they are in compliance with the law. You are also looking to see if there is anything you can do to help them.
5. Engaging Third-Party Auditors
If you don’t have the resources or expertise to do the audits yourself, you can hire a third-party audit firm. They specialize in doing audits. They have experience working in different countries and industries. There are several benefits to hiring a third-party audit firm:
- Impartiality: External auditors provide an unbiased assessment.
- Expertise: Experienced auditors are familiar with local laws, industry standards, and best practices.
- Efficiency: Third-party firms can often complete audits more quickly and thoroughly.
Some reputable third-party audit firms include SGS, Intertek, and Bureau Veritas, all of which have global operations and specific expertise in footwear and textile industries.
6. Conclusion
Conducting a supplier audit for slipper manufacturing plants is a critical step in ensuring that your suppliers meet the necessary quality, regulatory, and ethical standards. By following a structured approach to audits—covering preparation, on-site inspections, compliance assessments, and follow-up actions—you can significantly reduce risks in your supply chain and improve product quality.
Whether you conduct the audits internally or work with third-party professionals, the insights gained from these audits will help you make more informed purchasing decisions, leading to a more reliable and responsible supply chain. By ensuring that your suppliers are compliant with industry standards and ethical practices, you not only protect your company’s reputation but also contribute to building a sustainable and ethically sound supply chain.